Prozessorientierter Digitaler Zwilling in WAAM: Unterschied zwischen den Versionen
Reisch (Diskussion | Beiträge) Keine Bearbeitungszusammenfassung |
K (Kategorie geändert.) |
||
(28 dazwischenliegende Versionen von 2 Benutzern werden nicht angezeigt) | |||
Zeile 1: | Zeile 1: | ||
Der Digitale Zwilling ermöglicht die datengetriebene Prozessüberwachung und -regelung in additiven Fertigungsprozessen. | Der {{wp|Digitaler Zwilling|Digitale Zwilling}} ermöglicht die datengetriebene {{wp|Prozessüberwachung|Prozessüberwachung}} und -regelung in additiven Fertigungsprozessen. Darüber hinaus sind Anknüpfungspunkte an die Entwicklungsphase und die Qualitätssicherung des Endprodukt möglich. | ||
[[Datei:ÜberblickDTinWAAM.png|700px|thumb|Überblick über den prozessorientierten Digitalen Zwilling in [[WAAM]]]] | |||
Nachfolgend werden Kernergebnisse der Dissertationsarbeit „Prozessorientierter Digitaler Zwilling für die Additive Fertigung mittels Lichtbogenauftragsschweißen“ (Referenz: Reisch <ref name="multiple">R.T. Reisch, ''Prozessorientierter Digitaler Zwilling für die Additive Fertigung mittels Lichtbogenauftragsschweißen'', (TUM, 20xx), </ref>) vorgestellt. | |||
Für eine detaillierte Darstellung der einzelnen Themen sowie für eine Zitation / ein Referenzieren der nachfolgend vorgestellten Inhalte wird auf die veröffentlichte Fassung der Arbeit<ref name="multiple">R.T. Reisch, ''Prozessorientierter Digitaler Zwilling für die Additive Fertigung mittels Lichtbogenauftragsschweißen'', (TUM, 20xx), </ref> verwiesen | Für eine detaillierte Darstellung der einzelnen Themen sowie für eine Zitation / ein Referenzieren der nachfolgend vorgestellten Inhalte wird auf die veröffentlichte Fassung der Arbeit<ref name="multiple">R.T. Reisch, ''Prozessorientierter Digitaler Zwilling für die Additive Fertigung mittels Lichtbogenauftragsschweißen'', (TUM, 20xx), </ref> verwiesen; die nachfolgenden Abschnitte sind dieser Arbeit<ref name="multiple">R.T. Reisch, ''Prozessorientierter Digitaler Zwilling für die Additive Fertigung mittels Lichtbogenauftragsschweißen'', (TUM, 20xx), </ref> entnommen. | ||
== | ==Einleitung== | ||
[[ | Der [[Wire-Arc Additive Manufacturing]] (WAAM) Prozess ermöglicht die Fertigung großvolumiger Metallbauteile. | ||
Aufgrund der hohen Auftragsrate, der geringen Kosten und einer kostengünstigen Anlagentechnik findet dieser Prozess zunehmend Anwendung in der Industrie (Luft- und Raumfahrt, Automobilbau, Zugtechnik). Um den Prozess jedoch umfangreich zu industrialisieren ist eine höhere Prozessautonomie sowie eine Verringerung des erforderlichen Expertenwissens zur Anwendung erforderlich. <ref name="overview">R.T. Reisch, ''Roboter in der Additiven Fertigung'', (Technik in Bayern, 2021), </ref> | |||
Dieses Ziel kann mithilfe einer umfassenden Digitalisierung und Automatisierung des Prozesses erreicht werden. | |||
In dieser Arbeit wird zu diesem Zweck ein prozessorientierter Digitaler Zwilling für WAAM vorgestellt. | |||
<!-- Die animierte GIF-Datei wird nur in Originalgröße abgespielt; offenbar wird beim Erzeugen eines Thumbnails nur das erste Bild verwendet. --> | |||
[[Datei:WAAM_Highspeed.gif|828px|thumb|none|Highspeed-Video (GIF) des [[WAAM]]-Prozesses]] | |||
==Grundlagen und Stand der Technik== | |||
== | |||
Vorstellung der Grundlagen im Bereich der Additiven Fertigung, zum Digitalen Zwilling sowie im Bereich der Datenanalytik. Es wird unter anderem auf die Prozessüberwachung, die Prozessregelung, die Anomaliedetektion bei Zeitreihendaten und Evaluierungsmetriken eingegangen. Abschließend wird der Forschungsbedarf abgeleitet sowie die Hypothese aufgestellt, dass mithilfe eines kontextwahrnehmenden, autonomen und anpassungsfähigen Digitalen Zwilling der WAAM-Prozess industrialisiert werden kann. Daraus ergab sich folgende Forschungsfrage, welche innerhalb der Arbeit beantwortet wurde: | Vorstellung der Grundlagen im Bereich der Additiven Fertigung, zum Digitalen Zwilling sowie im Bereich der Datenanalytik. Es wird unter anderem auf die Prozessüberwachung, die Prozessregelung, die Anomaliedetektion bei Zeitreihendaten und Evaluierungsmetriken eingegangen. Abschließend wird der Forschungsbedarf abgeleitet sowie die Hypothese aufgestellt, dass mithilfe eines kontextwahrnehmenden, autonomen und anpassungsfähigen Digitalen Zwilling der WAAM-Prozess industrialisiert werden kann. Daraus ergab sich folgende Forschungsfrage, welche innerhalb der Arbeit beantwortet wurde: | ||
:„Wie können Kontextwahrnehmung, Autonomie und Anpassungsfähigkeit eines prozessorientierten Digitalen Zwillings für die additive Fertigung mittels Lichtbogenauftragsschweißen erreicht werden?“ | |||
== | ==Digitale Bauteil- und Prozessrepräsentation== | ||
Die digitale Bauteil- und Prozessrepräsentation erlaubt die Bereitstellung von Kontext für die Prozessüberwachung und die Prozessanpassung. | Die digitale Bauteil- und Prozessrepräsentation erlaubt die Bereitstellung von Kontext für die Prozessüberwachung und die Prozessanpassung. | ||
Zeile 36: | Zeile 30: | ||
* Zeitlicher Kontext | * Zeitlicher Kontext | ||
* Räumlicher Kontext | * Räumlicher Kontext | ||
Der Systemkontext wurde mithilfe eines OPC UA Informationsmodells sowie eines Prozesszustandsmodells bereitgehalten. | Der Systemkontext wurde mithilfe eines {{wp|OPC Unified Architecture|OPC UA}} Informationsmodells sowie eines Prozesszustandsmodells bereitgehalten. | ||
Die zeitliche Einordnung geschieht auf Basis einer zeitlichen Indexierung aller Dateninstanzen. Um den räumlichen Kontext bereitzustellen, wurde der Octree als räumliche Datenstruktur eingeführt. Alle Datenpunkte werden raumzeitindexiert. Zu Beginn des Aufbaus eines neuen Bauteils stellt der lediglich mit Simulationsdaten gefüllte Octree ein Digitales Modell dar (statischer Octree). Während des Prozesses werden abhängig vom Prozess weitere Datenpunkte eingeführt, sodass es sich um einen Digitalen Schatten des Bauteils handelt (dynamischer Octree). Auf Basis der Prozessanpassung und der damit einhergehenden bidirektionalen Datenanbindung entsteht in Kapitel 5 ein Digitaler Zwilling. | Die zeitliche Einordnung geschieht auf Basis einer zeitlichen Indexierung aller Dateninstanzen. Um den räumlichen Kontext bereitzustellen, wurde der {{wp|Octree|Octree}} als räumliche Datenstruktur eingeführt. Alle Datenpunkte werden raumzeitindexiert. Zu Beginn des Aufbaus eines neuen Bauteils stellt der lediglich mit Simulationsdaten gefüllte Octree ein Digitales Modell dar (statischer Octree). Während des Prozesses werden abhängig vom Prozess weitere Datenpunkte eingeführt, sodass es sich um einen Digitalen Schatten des Bauteils handelt (dynamischer Octree). Auf Basis der Prozessanpassung und der damit einhergehenden bidirektionalen Datenanbindung entsteht in Kapitel 5 ein Digitaler Zwilling.<ref name="anomaly2">R.T. Reisch, ''Context awareness in process monitoring of additive manufacturing using a digita twin'', (JAMP, 2022), </ref> | ||
Der Digitale Schatten kann als Informationsträger für Optimierungsschritte im CAD/CAM-Bereich sowie in der Qualitätssicherung eingesetzt werden. | Der Digitale Schatten kann als Informationsträger für Optimierungsschritte im CAD/CAM-Bereich sowie in der Qualitätssicherung eingesetzt werden. | ||
Zur Anbindung an die prozessvor- und nachgelagerten Schritte der Wertschöpfungskette wurde darüber hinaus eine Methodik entwickelt, mithilfe derer die räumliche Annotation zeitlicher Daten möglich ist. Die Labels können anschließend für das Training und die Evaluierung von Anomaliedetektions- und Defektklassifikationsalgorithmen eingesetzt werden. | Zur Anbindung an die prozessvor- und nachgelagerten Schritte der Wertschöpfungskette wurde darüber hinaus eine Methodik entwickelt, mithilfe derer die räumliche Annotation zeitlicher Daten möglich ist. Die Labels können anschließend für das Training und die Evaluierung von Anomaliedetektions- und Defektklassifikationsalgorithmen eingesetzt werden. <ref name="spatialannotation">R.T. Reisch, ''Spatial Annotation of Time Series for Data Driven Quality Assurance in Additive Manufacturing'', (CIRP ICME, 2022), </ref> | ||
== | ==Prozessmodellierung und -überwachung== | ||
[[Datei:Prozessdefekte_WAAM.PNG|600px|thumb|right|Defekte beim [[WAAM]]-Prozess]] | [[Datei:Prozessdefekte_WAAM.PNG|600px|thumb|right|Defekte beim [[WAAM]]-Prozess]] | ||
Die Prozessüberwachung ermöglicht die Erkennung von Instabilitäten und Defekten prozessparallel. Um ein grundlegendes Verständnis des Prozesses aufzubauen wurde der Prozess zunächst analysiert und eine Ursachen-Wirkungs-Analyse für Abweichungen in den Prozessdaten vorgenommen. Mithilfe dieser Informationen wurden geeignete Sensoren (Strom, Spannung, Drahtvorschub, Gasfluss, Spektrometer, Schweißkamera, Mikrofon) ausgewählt und der | Die Prozessüberwachung ermöglicht die Erkennung von Instabilitäten und Defekten prozessparallel. | ||
===Prozessmodellierung=== | |||
Um ein grundlegendes Verständnis des Prozesses aufzubauen wurde der Prozess zunächst analysiert und eine Ursachen-Wirkungs-Analyse für Abweichungen in den Prozessdaten vorgenommen. Mithilfe dieser Informationen wurden geeignete Sensoren (Strom, Spannung, Drahtvorschub, Gasfluss, Spektrometer, Schweißkamera, Mikrofon) ausgewählt und der WAAM-Prozess datengetrieben nachgebildet. | |||
===Anomaliedetektion=== | |||
Anomalien in den Daten wurden mithilfe von Anomaliedetektoren erkannt. Dazu wurde zunächst eine Methodik entwickelt, mit deren Hilfe ein geeigneter Detektor abhängig von den Zeitreihenmerkmalen der Daten ausgewählt werden kann. Es wurden sowohl wahrscheinlichkeits- und distanzbasierte (u.a. Isolation Forest), rekonstruktionsbasierte (u.a. Autoencoder) und vorhersagebasierte (u.a. Neuronale Netzwerke) Anomaliedetektoren betrachtet. Da der Autoencoder für die Spannungsdaten des WAAM-Prozesses sehr gute Ergebnisse lieferte, wurde dieser näher betrachtet. Die Architektur des Autoencoders wurde um ein externes Speichermodul erweitert, um verschiedene Konditionen (=Prozessparametersätze) abbilden zu können. Dieser Aufbau des Autoencoders ermöglichte darüber hinaus Metalernen, sodass eine Anpassungsfähigkeit an neue Prozessparameter erreicht wurde. | |||
<ref name="anomaly1">R.T. Reisch, ''Distance-Based Multivariate Anomaly Detection in Wire Arc Additive Manufacturing'', (IEEE ICMLA, 2021), </ref> <ref name="anomaly2">R.T. Reisch, ''Context awareness in process monitoring of additive manufacturing using a digita twin'', (JAMP, 2022), </ref> | |||
Mithilfe eines Metalernansatzes ( | ===Defektklassifikation=== | ||
Kontextwahrnehmung erhöhte die Genauigkeit der Klassifikation zum Teil erheblich. | Zur Defektklassifikation wurde je Defekt ein neuronales Netzwerk aufgebaut. Potentielle Defekte sind in der Abbildung [[Media:Prozessdefekte_WAAM.PNG|Defekte beim WAAM-Prozess]] dargestellt. | ||
Mithilfe eines Metalernansatzes („Model Agnostic Meta Learning“) war die Übertragung der erlernten datenbasierten Eigenschaften eines Defekte auf andere Prozessparameter und damit Anpassungsfähigkeit möglich. | |||
Kontextwahrnehmung erhöhte die Genauigkeit der Klassifikation zum Teil erheblich. | |||
Zuletzt wurden in diesem Kapitel Methoden zur Messung des Abstands zwischen Schweißbrenner und Bauteil vorgestellt. Dazu wurden drei Sensoren (Spannung, Spektrometer, Schweißkamera) betrachtet, Datenmerkmale extrahiert und eine Korrelationsanalyse mit dem Abstand vorgenommen. Trotz hoher Korrelationen für das Spektrometer wurde letztendlich auf Grund der geringeren Prozessparameterabhängigkeit der Messung die Schweißkamera genutzt. | ===Abstandsmessung=== | ||
Die in diesem Kapitel gewonnenen Informationen werden für den datengestützten Prozesseingriff verwendet. | Zuletzt wurden in diesem Kapitel Methoden zur Messung des Abstands zwischen Schweißbrenner und Bauteil vorgestellt. Dazu wurden drei Sensoren (Spannung, Spektrometer, Schweißkamera) betrachtet, Datenmerkmale extrahiert und eine Korrelationsanalyse mit dem Abstand zwischen Schweißbrenner und Bauteil vorgenommen. Trotz hoher Korrelationen für das Spektrometer wurde letztendlich auf Grund der geringeren Prozessparameterabhängigkeit der Messung die Schweißkamera als bevorzugter Sensor genutzt. <ref name="CLC">R.T. Reisch, ''Nozzle-to-Work Distance Measurement and Control in Wire Arc Additive Manufacturing'', (ESSE, 2021), </ref> | ||
Die in diesem Kapitel gewonnenen Informationen werden für den datengestützten Prozesseingriff verwendet. | |||
== | ==Datengestützter Prozesseingriff== | ||
[[Datei:CLC_WAAM.gif|700px|right|thumb|Messung der Distanz zwischen Schweißbrenner und Bauteil beim [[WAAM]]-Prozess als Eingangsgröße für die Prozessregelung]] | [[Datei:CLC_WAAM.gif|700px|right|thumb|Messung der Distanz zwischen Schweißbrenner und Bauteil beim [[WAAM]]-Prozess als Eingangsgröße für die Prozessregelung]] | ||
Um die Prozessstabilität zu erhöhen werden Prozesseingriffe vorgenommen. | Um die Prozessstabilität zu erhöhen, werden Prozesseingriffe vorgenommen. Dabei kann es sich einerseits um eine Prozesswarnung, einen Prozessstopp, um eine Prozessregelung oder um eine präskriptive Prozessparameteranpassung handeln. | ||
===Systemidentifikation=== | ===Systemidentifikation=== | ||
Zunächst wurde eine Systemidentifikation vorgenommen, die die Prozessparameter (Schweißgeschwindigkeit und Drahtvorschub) mit der Schweißnahtgeometrie (Schweißnahtbreite und -höhe) in Relation setzte. Es zeigte sich eine hohe negative Korrelation nach Pearson (-0,900) zwischen Schweißgeschwindigkeit und Schweißnahthöhe und eine hohe positive Korrelation (0,859) zwischen Drahtvorschub und Schweißnahtbreite. Weiterhin konnte eine Korrelation zwischen Schweißgeschwindigkeit und Schweißnahtbreite (-0,388) erfasst werden. Zwischen Drahtvorschub und Schweißnahthöhe war lediglich eine geringfügige Korrelation zu sehen (-0,093). | Zunächst wurde eine Systemidentifikation vorgenommen, die die Prozessparameter (Schweißgeschwindigkeit und Drahtvorschub) mit der Schweißnahtgeometrie (Schweißnahtbreite und -höhe) in Relation setzte. Es zeigte sich eine hohe negative Korrelation nach {{wp|Korrelationskoeffizient|Pearson}} (-0,900) zwischen Schweißgeschwindigkeit und Schweißnahthöhe und eine hohe positive Korrelation (0,859) zwischen Drahtvorschub und Schweißnahtbreite. Weiterhin konnte eine Korrelation zwischen Schweißgeschwindigkeit und Schweißnahtbreite (-0,388) erfasst werden. Zwischen Drahtvorschub und Schweißnahthöhe war lediglich eine geringfügige Korrelation zu sehen (-0,093). <ref name="CLC">R.T. Reisch, ''Nozzle-to-Work Distance Measurement and Control in Wire Arc Additive Manufacturing'', (ESSE, 2021), </ref> | ||
===Prozessregelung=== | ===Prozessregelung=== | ||
Mithilfe dieser Ergebnisse sowie den Messwerten des Abstands aus dem vorherigen Kapitel wird eine Prozessregelung aufgebaut. Dabei wird die Schweißgeschwindigkeit genutzt, um die Schweißbadhöhe anzupassen und dadurch den Abstand zwischen Schweißbrenner und Bauteil konstant zu halten. Mithilfe einer Anpassung der Drahtvorschubgeschwindigkeit konnte die Schweißnahtbreite trotz Änderung der Schweißgeschwindigkeit konstant gehalten werden. Die Abstandsregelung ermöglichte den Aufbau komplexer Bauteile mit Multiachsoperationen ohne vorherige Prozessparameteroptimierung beim ersten Versuch. | Mithilfe dieser Ergebnisse sowie den Messwerten des Abstands aus dem vorherigen Kapitel wird eine Prozessregelung aufgebaut. Dabei wird die Schweißgeschwindigkeit genutzt, um die Schweißbadhöhe anzupassen und dadurch den Abstand zwischen Schweißbrenner und Bauteil konstant zu halten. Mithilfe einer Anpassung der Drahtvorschubgeschwindigkeit konnte die Schweißnahtbreite trotz Änderung der Schweißgeschwindigkeit konstant gehalten werden. Die Abstandsregelung ermöglichte den Aufbau komplexer Bauteile mit Multiachsoperationen ohne vorherige Prozessparameteroptimierung beim ersten Versuch. <ref name="CLC">R.T. Reisch, ''Nozzle-to-Work Distance Measurement and Control in Wire Arc Additive Manufacturing'', (ESSE, 2021), </ref> | ||
===Präskriptive Prozessparameteranpassung=== | ===Präskriptive Prozessparameteranpassung=== | ||
Im [[WAAM]]-Prozess kann es jederzeit zu Instabilitäten kommen. Um die daraus resultierenden Defekte zu kompensieren sowie Folgedefekte zu vermeiden, wurde eine präskriptive Prozessparameteranpassung vorgestellt. Sie nutzt die Kontextwahrnehmung der Bauteil- und Prozessrepräsentation sowie die Anpassungsfähigkeit der Prozessüberwachung um Autonomie zu erreichen. Zunächst wurde eine Positionsvorhersage durchgeführt und der zukünftig Kontext analysiert. Abhängig vom Kontext wurde ein Prozesseingriff vorgenommen, indem die Prozessparameter zum passenden Zeitpunkt so angepasst wurden, dass der Defekt kompensiert wurde. Die Methodik konnte anhand der Kompensation eines Unstetigkeitsdefekt verifiziert werden. | Im [[WAAM]]-Prozess kann es jederzeit zu Instabilitäten kommen. Um die daraus resultierenden Defekte zu kompensieren sowie Folgedefekte zu vermeiden, wurde eine präskriptive Prozessparameteranpassung vorgestellt. Sie nutzt die Kontextwahrnehmung der Bauteil- und Prozessrepräsentation sowie die Anpassungsfähigkeit der Prozessüberwachung um Autonomie zu erreichen. Zunächst wurde eine Positionsvorhersage durchgeführt und der zukünftig Kontext analysiert. Abhängig vom Kontext wurde ein Prozesseingriff vorgenommen, indem die Prozessparameter zum passenden Zeitpunkt so angepasst wurden, dass der Defekt kompensiert wurde. Die Methodik konnte anhand der Kompensation eines Unstetigkeitsdefekt verifiziert werden. <ref name="prescriptive">R.T. Reisch, ''Prescriptive Analytics - A Smart Manufacturing System for First-Time-Right Printing in Wire Arc Additive Manufacturing using a Digital Twin'', (CIRP ICME, 2022), </ref> | ||
== | ==Erprobung in der industriellen Praxis== | ||
Zur Validierung wurde der Einsatz des Digitalen Zwillings in der industriellen Praxis in einem | Zur Validierung wurde der Einsatz des Digitalen Zwillings in der industriellen Praxis in einem WAAM-System anhand des Aufbaus zweier Bauteile erprobt. | ||
Der Digitale Zwilling wurde dazu als Teil eines intelligenten Fertigungssystems prototypische implementiert. | Der Digitale Zwilling wurde dazu als Teil eines intelligenten Fertigungssystems prototypische implementiert. | ||
Beim Aufbau der zwei Validierungsbauteile konnte mithilfe des Digitalen Zwillings die Kausalkette für Defekte hergeleitet werden. Weiterhin wurden im Prozess Anpassungen vorgenommen. Dadurch konnte ein Mehrwert für die Prozessplanung, die Anlagenbedienenden und Qualitätsverantwortliche gezeigt werden. Zuletzt erfolgt eine anforderungsbezogene Bewertung des Digitalen Zwillings und die abschließende Beantwortung der gestellten Forschungsfrage. | Beim Aufbau der zwei Validierungsbauteile konnte mithilfe des Digitalen Zwillings die Kausalkette für Defekte hergeleitet werden. Weiterhin wurden im Prozess Anpassungen vorgenommen. Dadurch konnte ein Mehrwert für die Prozessplanung, die Anlagenbedienenden und Qualitätsverantwortliche gezeigt werden. Zuletzt erfolgt eine anforderungsbezogene Bewertung des Digitalen Zwillings und die abschließende Beantwortung der gestellten Forschungsfrage. | ||
<gallery widths=400px> | |||
Datei:DigitalerZwillingBionischerArm.png|Digitaler Zwilling des bionischen Arms (Copyright: Reisch) | |||
Datei:robotbased_WAAM.jpg|Roboterbasiertes WAAM-Setup am Forschungs- und Vorentwicklungsstandort der [[Siemens AG]] in München | |||
</gallery> | |||
== | ==Schlussfolgerung und Ausblick== | ||
Im letzten Kapitel der Arbeit wurde die Arbeit zusammengefasst und die Übertragbarkeit der vorgestellten Methoden auf weitere Felder betrachtet. Weiterhin wurde ein Ausblick im Bezug auf den prozessorientierten Zwilling für die Additive Fertigung mittels Lichtbogenauftragsschweißen gegeben.. | |||
==Referenzen== | ==Referenzen== | ||
[[Kategorie:Veröffentlichungsreif]] |
Aktuelle Version vom 10. Februar 2023, 13:39 Uhr
Der ➭Digitale Zwilling ermöglicht die datengetriebene ➭Prozessüberwachung und -regelung in additiven Fertigungsprozessen. Darüber hinaus sind Anknüpfungspunkte an die Entwicklungsphase und die Qualitätssicherung des Endprodukt möglich.
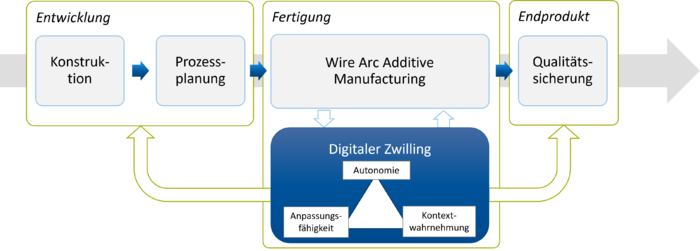
Nachfolgend werden Kernergebnisse der Dissertationsarbeit „Prozessorientierter Digitaler Zwilling für die Additive Fertigung mittels Lichtbogenauftragsschweißen“ (Referenz: Reisch [1]) vorgestellt.
Für eine detaillierte Darstellung der einzelnen Themen sowie für eine Zitation / ein Referenzieren der nachfolgend vorgestellten Inhalte wird auf die veröffentlichte Fassung der Arbeit[1] verwiesen; die nachfolgenden Abschnitte sind dieser Arbeit[1] entnommen.
Einleitung
Der Wire-Arc Additive Manufacturing (WAAM) Prozess ermöglicht die Fertigung großvolumiger Metallbauteile.
Aufgrund der hohen Auftragsrate, der geringen Kosten und einer kostengünstigen Anlagentechnik findet dieser Prozess zunehmend Anwendung in der Industrie (Luft- und Raumfahrt, Automobilbau, Zugtechnik). Um den Prozess jedoch umfangreich zu industrialisieren ist eine höhere Prozessautonomie sowie eine Verringerung des erforderlichen Expertenwissens zur Anwendung erforderlich. [2] Dieses Ziel kann mithilfe einer umfassenden Digitalisierung und Automatisierung des Prozesses erreicht werden. In dieser Arbeit wird zu diesem Zweck ein prozessorientierter Digitaler Zwilling für WAAM vorgestellt.
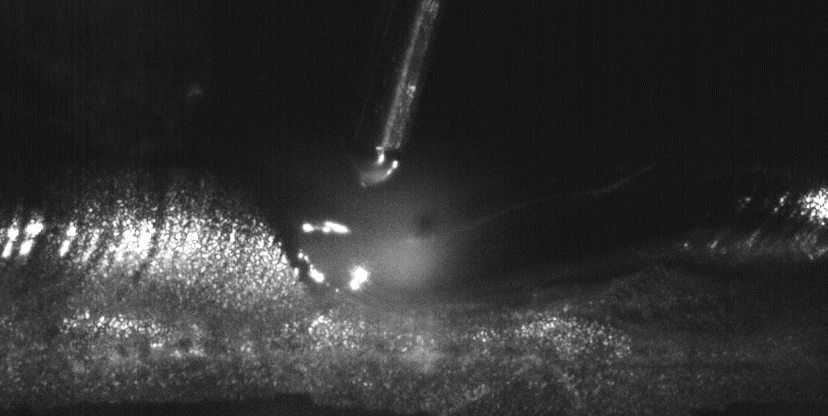
Grundlagen und Stand der Technik
Vorstellung der Grundlagen im Bereich der Additiven Fertigung, zum Digitalen Zwilling sowie im Bereich der Datenanalytik. Es wird unter anderem auf die Prozessüberwachung, die Prozessregelung, die Anomaliedetektion bei Zeitreihendaten und Evaluierungsmetriken eingegangen. Abschließend wird der Forschungsbedarf abgeleitet sowie die Hypothese aufgestellt, dass mithilfe eines kontextwahrnehmenden, autonomen und anpassungsfähigen Digitalen Zwilling der WAAM-Prozess industrialisiert werden kann. Daraus ergab sich folgende Forschungsfrage, welche innerhalb der Arbeit beantwortet wurde:
- „Wie können Kontextwahrnehmung, Autonomie und Anpassungsfähigkeit eines prozessorientierten Digitalen Zwillings für die additive Fertigung mittels Lichtbogenauftragsschweißen erreicht werden?“
Digitale Bauteil- und Prozessrepräsentation
Die digitale Bauteil- und Prozessrepräsentation erlaubt die Bereitstellung von Kontext für die Prozessüberwachung und die Prozessanpassung. Dazu wurde der Kontext zunächst in drei Bereiche eingeteilt:
- Systemkontext
- Zeitlicher Kontext
- Räumlicher Kontext
Der Systemkontext wurde mithilfe eines ➭OPC UA Informationsmodells sowie eines Prozesszustandsmodells bereitgehalten. Die zeitliche Einordnung geschieht auf Basis einer zeitlichen Indexierung aller Dateninstanzen. Um den räumlichen Kontext bereitzustellen, wurde der ➭Octree als räumliche Datenstruktur eingeführt. Alle Datenpunkte werden raumzeitindexiert. Zu Beginn des Aufbaus eines neuen Bauteils stellt der lediglich mit Simulationsdaten gefüllte Octree ein Digitales Modell dar (statischer Octree). Während des Prozesses werden abhängig vom Prozess weitere Datenpunkte eingeführt, sodass es sich um einen Digitalen Schatten des Bauteils handelt (dynamischer Octree). Auf Basis der Prozessanpassung und der damit einhergehenden bidirektionalen Datenanbindung entsteht in Kapitel 5 ein Digitaler Zwilling.[3]
Der Digitale Schatten kann als Informationsträger für Optimierungsschritte im CAD/CAM-Bereich sowie in der Qualitätssicherung eingesetzt werden. Zur Anbindung an die prozessvor- und nachgelagerten Schritte der Wertschöpfungskette wurde darüber hinaus eine Methodik entwickelt, mithilfe derer die räumliche Annotation zeitlicher Daten möglich ist. Die Labels können anschließend für das Training und die Evaluierung von Anomaliedetektions- und Defektklassifikationsalgorithmen eingesetzt werden. [4]
Prozessmodellierung und -überwachung
Die Prozessüberwachung ermöglicht die Erkennung von Instabilitäten und Defekten prozessparallel.
Prozessmodellierung
Um ein grundlegendes Verständnis des Prozesses aufzubauen wurde der Prozess zunächst analysiert und eine Ursachen-Wirkungs-Analyse für Abweichungen in den Prozessdaten vorgenommen. Mithilfe dieser Informationen wurden geeignete Sensoren (Strom, Spannung, Drahtvorschub, Gasfluss, Spektrometer, Schweißkamera, Mikrofon) ausgewählt und der WAAM-Prozess datengetrieben nachgebildet.
Anomaliedetektion
Anomalien in den Daten wurden mithilfe von Anomaliedetektoren erkannt. Dazu wurde zunächst eine Methodik entwickelt, mit deren Hilfe ein geeigneter Detektor abhängig von den Zeitreihenmerkmalen der Daten ausgewählt werden kann. Es wurden sowohl wahrscheinlichkeits- und distanzbasierte (u.a. Isolation Forest), rekonstruktionsbasierte (u.a. Autoencoder) und vorhersagebasierte (u.a. Neuronale Netzwerke) Anomaliedetektoren betrachtet. Da der Autoencoder für die Spannungsdaten des WAAM-Prozesses sehr gute Ergebnisse lieferte, wurde dieser näher betrachtet. Die Architektur des Autoencoders wurde um ein externes Speichermodul erweitert, um verschiedene Konditionen (=Prozessparametersätze) abbilden zu können. Dieser Aufbau des Autoencoders ermöglichte darüber hinaus Metalernen, sodass eine Anpassungsfähigkeit an neue Prozessparameter erreicht wurde. [5] [3]
Defektklassifikation
Zur Defektklassifikation wurde je Defekt ein neuronales Netzwerk aufgebaut. Potentielle Defekte sind in der Abbildung Defekte beim WAAM-Prozess dargestellt. Mithilfe eines Metalernansatzes („Model Agnostic Meta Learning“) war die Übertragung der erlernten datenbasierten Eigenschaften eines Defekte auf andere Prozessparameter und damit Anpassungsfähigkeit möglich. Kontextwahrnehmung erhöhte die Genauigkeit der Klassifikation zum Teil erheblich.
Abstandsmessung
Zuletzt wurden in diesem Kapitel Methoden zur Messung des Abstands zwischen Schweißbrenner und Bauteil vorgestellt. Dazu wurden drei Sensoren (Spannung, Spektrometer, Schweißkamera) betrachtet, Datenmerkmale extrahiert und eine Korrelationsanalyse mit dem Abstand zwischen Schweißbrenner und Bauteil vorgenommen. Trotz hoher Korrelationen für das Spektrometer wurde letztendlich auf Grund der geringeren Prozessparameterabhängigkeit der Messung die Schweißkamera als bevorzugter Sensor genutzt. [6] Die in diesem Kapitel gewonnenen Informationen werden für den datengestützten Prozesseingriff verwendet.
Datengestützter Prozesseingriff
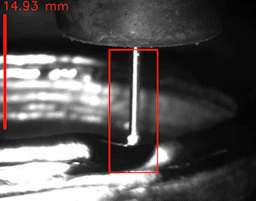
Um die Prozessstabilität zu erhöhen, werden Prozesseingriffe vorgenommen. Dabei kann es sich einerseits um eine Prozesswarnung, einen Prozessstopp, um eine Prozessregelung oder um eine präskriptive Prozessparameteranpassung handeln.
Systemidentifikation
Zunächst wurde eine Systemidentifikation vorgenommen, die die Prozessparameter (Schweißgeschwindigkeit und Drahtvorschub) mit der Schweißnahtgeometrie (Schweißnahtbreite und -höhe) in Relation setzte. Es zeigte sich eine hohe negative Korrelation nach ➭Pearson (-0,900) zwischen Schweißgeschwindigkeit und Schweißnahthöhe und eine hohe positive Korrelation (0,859) zwischen Drahtvorschub und Schweißnahtbreite. Weiterhin konnte eine Korrelation zwischen Schweißgeschwindigkeit und Schweißnahtbreite (-0,388) erfasst werden. Zwischen Drahtvorschub und Schweißnahthöhe war lediglich eine geringfügige Korrelation zu sehen (-0,093). [6]
Prozessregelung
Mithilfe dieser Ergebnisse sowie den Messwerten des Abstands aus dem vorherigen Kapitel wird eine Prozessregelung aufgebaut. Dabei wird die Schweißgeschwindigkeit genutzt, um die Schweißbadhöhe anzupassen und dadurch den Abstand zwischen Schweißbrenner und Bauteil konstant zu halten. Mithilfe einer Anpassung der Drahtvorschubgeschwindigkeit konnte die Schweißnahtbreite trotz Änderung der Schweißgeschwindigkeit konstant gehalten werden. Die Abstandsregelung ermöglichte den Aufbau komplexer Bauteile mit Multiachsoperationen ohne vorherige Prozessparameteroptimierung beim ersten Versuch. [6]
Präskriptive Prozessparameteranpassung
Im WAAM-Prozess kann es jederzeit zu Instabilitäten kommen. Um die daraus resultierenden Defekte zu kompensieren sowie Folgedefekte zu vermeiden, wurde eine präskriptive Prozessparameteranpassung vorgestellt. Sie nutzt die Kontextwahrnehmung der Bauteil- und Prozessrepräsentation sowie die Anpassungsfähigkeit der Prozessüberwachung um Autonomie zu erreichen. Zunächst wurde eine Positionsvorhersage durchgeführt und der zukünftig Kontext analysiert. Abhängig vom Kontext wurde ein Prozesseingriff vorgenommen, indem die Prozessparameter zum passenden Zeitpunkt so angepasst wurden, dass der Defekt kompensiert wurde. Die Methodik konnte anhand der Kompensation eines Unstetigkeitsdefekt verifiziert werden. [7]
Erprobung in der industriellen Praxis
Zur Validierung wurde der Einsatz des Digitalen Zwillings in der industriellen Praxis in einem WAAM-System anhand des Aufbaus zweier Bauteile erprobt. Der Digitale Zwilling wurde dazu als Teil eines intelligenten Fertigungssystems prototypische implementiert. Beim Aufbau der zwei Validierungsbauteile konnte mithilfe des Digitalen Zwillings die Kausalkette für Defekte hergeleitet werden. Weiterhin wurden im Prozess Anpassungen vorgenommen. Dadurch konnte ein Mehrwert für die Prozessplanung, die Anlagenbedienenden und Qualitätsverantwortliche gezeigt werden. Zuletzt erfolgt eine anforderungsbezogene Bewertung des Digitalen Zwillings und die abschließende Beantwortung der gestellten Forschungsfrage.
Roboterbasiertes WAAM-Setup am Forschungs- und Vorentwicklungsstandort der Siemens AG in München
Schlussfolgerung und Ausblick
Im letzten Kapitel der Arbeit wurde die Arbeit zusammengefasst und die Übertragbarkeit der vorgestellten Methoden auf weitere Felder betrachtet. Weiterhin wurde ein Ausblick im Bezug auf den prozessorientierten Zwilling für die Additive Fertigung mittels Lichtbogenauftragsschweißen gegeben..
Referenzen
- ↑ 1,0 1,1 1,2 R.T. Reisch, Prozessorientierter Digitaler Zwilling für die Additive Fertigung mittels Lichtbogenauftragsschweißen, (TUM, 20xx),
- ↑ R.T. Reisch, Roboter in der Additiven Fertigung, (Technik in Bayern, 2021),
- ↑ 3,0 3,1 R.T. Reisch, Context awareness in process monitoring of additive manufacturing using a digita twin, (JAMP, 2022),
- ↑ R.T. Reisch, Spatial Annotation of Time Series for Data Driven Quality Assurance in Additive Manufacturing, (CIRP ICME, 2022),
- ↑ R.T. Reisch, Distance-Based Multivariate Anomaly Detection in Wire Arc Additive Manufacturing, (IEEE ICMLA, 2021),
- ↑ 6,0 6,1 6,2 R.T. Reisch, Nozzle-to-Work Distance Measurement and Control in Wire Arc Additive Manufacturing, (ESSE, 2021),
- ↑ R.T. Reisch, Prescriptive Analytics - A Smart Manufacturing System for First-Time-Right Printing in Wire Arc Additive Manufacturing using a Digital Twin, (CIRP ICME, 2022),