Edge-basierte Geometrieerfassung: Unterschied zwischen den Versionen
(Bild zur Konzept-Übersicht ergänzt) |
(Bilder der LLT-Sensoren in dem beiden Zielsystemen ergänzt; Unterpunkte in Artikel eingefügt) |
||
Zeile 2: | Zeile 2: | ||
[[Datei:Geom-Erf-uebersicht.png|500px|right|thumb|Konzept-Übersicht [[Edge-basierte Geometrieerfassung]]]] | [[Datei:Geom-Erf-uebersicht.png|500px|right|thumb|Konzept-Übersicht [[Edge-basierte Geometrieerfassung]]]] | ||
[[Datei:LLT-mounting_mch.jpg|400px|right|thumb|Laser-Linien-Sensor im Zielsystem in München]] | |||
Im Rahmen der Aktivitäten zur [[Datenerfassung und Prozessregelung im WAAM Prozess]] wurde durch die Siemens AG an der Entwicklung eines Systems zur prozessbegleitenden Überwachung der geometrischen Werkstückqualität gearbeitet (Abbildung 12). Im Gegensatz zu den an der [[FHWS]] durchgeführten Aktivitäten zur Qualitätsüberwachung liegt der Fokus hier auf mehrachsigen AM-Prozessen ([[WAAM]], [[DED]]/[[LMD]]), die typischerweise von einer numerischen Bahnsteuerung (z. B. Sinumerik) geregelt und teilweise auch in Kombination mit subtraktiven Bearbeitungsmöglichkeiten in einer Maschine vereint werden. Mit Hilfe eines an der Maschinenkinematik mitgeführten Laserlinienscanners entsteht eine dreidimensionale Punktewolke der Werkstückoberfläche, die während des Prozesses fortlaufend aktualisiert wird. Alternativ werden konzeptionell auch Tiefenkameras und Punktlaser unterstützt. | Im Rahmen der Aktivitäten zur [[Datenerfassung und Prozessregelung im WAAM Prozess]] wurde durch die Siemens AG an der Entwicklung eines Systems zur prozessbegleitenden Überwachung der geometrischen Werkstückqualität gearbeitet (Abbildung 12). Im Gegensatz zu den an der [[FHWS]] durchgeführten Aktivitäten zur Qualitätsüberwachung liegt der Fokus hier auf mehrachsigen AM-Prozessen ([[WAAM]], [[DED]]/[[LMD]]), die typischerweise von einer numerischen Bahnsteuerung (z. B. Sinumerik) geregelt und teilweise auch in Kombination mit subtraktiven Bearbeitungsmöglichkeiten in einer Maschine vereint werden. Mit Hilfe eines an der Maschinenkinematik mitgeführten Laserlinienscanners entsteht eine dreidimensionale Punktewolke der Werkstückoberfläche, die während des Prozesses fortlaufend aktualisiert wird. Alternativ werden konzeptionell auch Tiefenkameras und Punktlaser unterstützt. | ||
Zeile 11: | Zeile 13: | ||
# Andererseits ist eine Überwachung geometrisch tolerierter Werkstückfeatures möglich, sodass fehlerhafte Prozessläufe frühzeitig erkannt und korrigiert bzw. abgebrochen werden können. Hierzu wurde eine Schnittstelle geschaffen, um die nominelle Werkstückgeometrie inklusive der {{wp|Toleranz_(Technik)#Fertigungstoleranzen|ISO Toleranzinformationen}} (z. B. Ebenheit) direkt aus der Konstruktionsumgebung auf die Maschine zu transferieren. Abweichungen in Form und Lage werden dem Bedienpersonal über eine Web-basierte Bedienoberfläche signalisiert. | # Andererseits ist eine Überwachung geometrisch tolerierter Werkstückfeatures möglich, sodass fehlerhafte Prozessläufe frühzeitig erkannt und korrigiert bzw. abgebrochen werden können. Hierzu wurde eine Schnittstelle geschaffen, um die nominelle Werkstückgeometrie inklusive der {{wp|Toleranz_(Technik)#Fertigungstoleranzen|ISO Toleranzinformationen}} (z. B. Ebenheit) direkt aus der Konstruktionsumgebung auf die Maschine zu transferieren. Abweichungen in Form und Lage werden dem Bedienpersonal über eine Web-basierte Bedienoberfläche signalisiert. | ||
== Implementierungen und | == Einschränkung des Lösungsraumes und gewähltes Lösungskonzept == | ||
{{Todo|... ergänzen ...}} | |||
== Implementierungen und Zielsysteme == | |||
[[Datei:LLT-mounting_nbg.jpg|300px|right|thumb|Laser-Linien-Sensor im Testsystem in Nürnberg]] | |||
Als Zielsystem im Projekt wurde das unter [[Wire-Arc_Additive_Manufacturing#Aufbau_einer_WAAM-Fertigungsanlage|Aufbau einer WAAM-Fertigungsanlage]] beschriebene Robotersystem mit Sinumerik-Steuerung gewählt. Aufgrund der besseren räumlichen und zeitlichen Verfügbarkeit, insbesondere unter den Bedingungen der Covid-Pandemie, wurden die meisten Implementierungen an einem 5-Achs-FDM-Forschungssystem der Siemens AG in Nürnberg entwickelt und erst im späteren Verlauf des Projektes so weit wie möglich auf das [[WAAM]]-System übertragen. | Als Zielsystem im Projekt wurde das unter [[Wire-Arc_Additive_Manufacturing#Aufbau_einer_WAAM-Fertigungsanlage|Aufbau einer WAAM-Fertigungsanlage]] beschriebene Robotersystem mit Sinumerik-Steuerung gewählt. Aufgrund der besseren räumlichen und zeitlichen Verfügbarkeit, insbesondere unter den Bedingungen der Covid-Pandemie, wurden die meisten Implementierungen an einem 5-Achs-FDM-Forschungssystem der Siemens AG in Nürnberg entwickelt und erst im späteren Verlauf des Projektes so weit wie möglich auf das [[WAAM]]-System übertragen. |
Aktuelle Version vom 21. Dezember 2022, 13:58 Uhr
Überblick
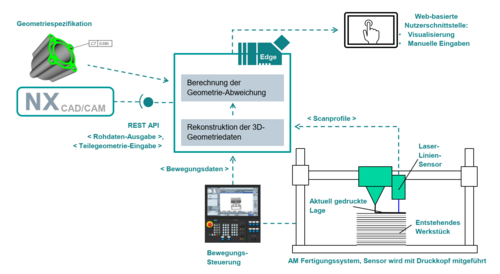
Im Rahmen der Aktivitäten zur Datenerfassung und Prozessregelung im WAAM Prozess wurde durch die Siemens AG an der Entwicklung eines Systems zur prozessbegleitenden Überwachung der geometrischen Werkstückqualität gearbeitet (Abbildung 12). Im Gegensatz zu den an der FHWS durchgeführten Aktivitäten zur Qualitätsüberwachung liegt der Fokus hier auf mehrachsigen AM-Prozessen (WAAM, DED/LMD), die typischerweise von einer numerischen Bahnsteuerung (z. B. Sinumerik) geregelt und teilweise auch in Kombination mit subtraktiven Bearbeitungsmöglichkeiten in einer Maschine vereint werden. Mit Hilfe eines an der Maschinenkinematik mitgeführten Laserlinienscanners entsteht eine dreidimensionale Punktewolke der Werkstückoberfläche, die während des Prozesses fortlaufend aktualisiert wird. Alternativ werden konzeptionell auch Tiefenkameras und Punktlaser unterstützt.
Anwendungsmöglichkeiten
Es ergeben sich zwei für die additive Fertigung relevante Anwendungsmöglichkeiten:
- Zum einen lassen sich bestehende Werkstücke in der späteren Bearbeitungsaufspannung als Grundlage zur Planung von Additivoperationen im CAM System digitalisieren. Dies ist besonders für AM gestützte Reparaturverfahren („Füllen schadhafter Werkstückbereiche“) oder das Andrucken von Formelementen an konventionell gefertigte Rohteile hilfreich.
- Andererseits ist eine Überwachung geometrisch tolerierter Werkstückfeatures möglich, sodass fehlerhafte Prozessläufe frühzeitig erkannt und korrigiert bzw. abgebrochen werden können. Hierzu wurde eine Schnittstelle geschaffen, um die nominelle Werkstückgeometrie inklusive der ➭ISO Toleranzinformationen (z. B. Ebenheit) direkt aus der Konstruktionsumgebung auf die Maschine zu transferieren. Abweichungen in Form und Lage werden dem Bedienpersonal über eine Web-basierte Bedienoberfläche signalisiert.
Einschränkung des Lösungsraumes und gewähltes Lösungskonzept
🚧 ❬... ergänzen ...❭
Implementierungen und Zielsysteme
Als Zielsystem im Projekt wurde das unter Aufbau einer WAAM-Fertigungsanlage beschriebene Robotersystem mit Sinumerik-Steuerung gewählt. Aufgrund der besseren räumlichen und zeitlichen Verfügbarkeit, insbesondere unter den Bedingungen der Covid-Pandemie, wurden die meisten Implementierungen an einem 5-Achs-FDM-Forschungssystem der Siemens AG in Nürnberg entwickelt und erst im späteren Verlauf des Projektes so weit wie möglich auf das WAAM-System übertragen.
🚧 ❬... ergänzen ...❭
Ausblick zur wirtschaftlichen Verwendbarkeit
Das entwickelte System basiert auf der ➭Edge-Computing Plattform der Siemens AG für den Werkzeugmaschinensektor [1] und hat damit gute Chance auf eine wirtschaftliche Verwertung. Der im Projekt gewählte, generische Ansatz mit weitgehender Unabhängigkeit von Sensor-Typ und Hersteller hat dabei aber eine Reihe von Herausforderungen aufgezeigt, die einer unmittelbaren Produktumsetzung im Wege stehen. Insbesondere erfordern die Synchronisierung der Sensorinformationen mit den Bewegungsdaten und die Datenverarbeitung zur Berechnung der Gestaltabweichungen auf Grundlage der Rohdaten noch weitere Forschungsarbeit.
- ↑ Siemens AG: Industrial Edge für Werkzeugmaschinen, URL: https://www.siemens.com/de/de/produkte/automatisierung/themenfelder/industrial-edge/werkzeugmaschinen.html