Wire-Arc Additive Manufacturing: Unterschied zwischen den Versionen
K (→Wertschöpfungskette: Unterstriche entfernt) |
K (In die große Wikipedia verlinkt.) |
||
Zeile 1: | Zeile 1: | ||
'''Wire-Arc Additive Manufacturing''' (kurz WAAM, dt. Lichtbogendrahtauftragsschweißen) ist ein Verfahren zur Additiven Fertigung, welches einen Draht und einen Lichtbogen nutzt, um Material aufzutragen und dadurch Bauteile aufzubauen. Das Verfahren ermöglicht eine kosteneffiziente Fertigung großvolumiger metallischer Bauteile. | '''Wire-Arc Additive Manufacturing''' (kurz WAAM, dt. Lichtbogendrahtauftragsschweißen) ist ein Verfahren zur Additiven Fertigung, welches einen Draht und einen Lichtbogen nutzt, um Material aufzutragen und dadurch Bauteile aufzubauen. WAAM ist eine automatisierte Form des [[de.wikipedia:Auftragschweißen|Auftragschweißen]]s. Das Verfahren ermöglicht eine kosteneffiziente Fertigung großvolumiger metallischer Bauteile. | ||
Weitere Informationen zu | Weitere Informationen zu WAAM können der Dissertationsarbeit [[Prozessorientierter Digitaler Zwilling in WAAM]] <ref name="multiple">R.T. Reisch, ''Prozessorientierter Digitaler Zwilling für die Additive Fertigung mittels Lichtbogenauftragsschweißen'', (TUM, 20xx), </ref> entnommen werden. | ||
==Überblick== | ==Überblick== |
Version vom 2. Dezember 2022, 09:48 Uhr
Wire-Arc Additive Manufacturing (kurz WAAM, dt. Lichtbogendrahtauftragsschweißen) ist ein Verfahren zur Additiven Fertigung, welches einen Draht und einen Lichtbogen nutzt, um Material aufzutragen und dadurch Bauteile aufzubauen. WAAM ist eine automatisierte Form des Auftragschweißens. Das Verfahren ermöglicht eine kosteneffiziente Fertigung großvolumiger metallischer Bauteile.
Weitere Informationen zu WAAM können der Dissertationsarbeit Prozessorientierter Digitaler Zwilling in WAAM [1] entnommen werden.
Überblick
Der WAAM-Prozess zeichnet sich durch hohe Auftragsraten und geringe Fertigungskosten aus. Die Materialnutzung ist hoch und die Investitionskosten sowie die Kosten des Ausgangsmaterials sind niedrig. Die Materialeigenschaften sind sehr gut. Die erreichbare Genauigkeit und Teilekomplexität ist jedoch geringer als bei anderen additiven Fertigungsverfahren wie L-PBF oder andere pulverbettbasierte Verfahren. Zudem ist der Nachbearbeitungsaufwand hoch.
Prozess
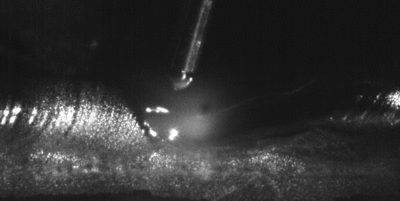
Im WAAM-Prozess können verschiedene Schweißverfahren eingesetzt werden:
- Metall-Schutzgas-Schweißen
- Wolfram-Inertgas-Schweißen
- Plasmaschweißen
In vielen Fällen wird der sogenannte CMT-Prozess genutzt, da hier der Wärmeeintrag auf Grund eines oszillierenden Drahts gering ist. Der CMT-Prozess ist ein wellenförmig kontrolliertes Schweißverfahren, in welchem die Strom- und Spannungsverläufe kontrolliert werden. Er teilt sich ein in drei Phasen:
- Spitzenstromphase: Zündung des Lichtbogens
- Hintergrundstromphase: Bewegung des Drahts in Richtung des Schmelzbads
- Kurzschlussphase: Ablegen des gebildeten Tropfens im Schmelzbads und Rückziehbewegung
Der Prozess ist in dem Hochgeschwindigkeitsvideo Media:WAAM_Highspeed.gif dargestellt. Als Materialien können Stahl, Aluminium, Titan sowie weitere schweißbare Materialien genutzt werden.
Aufbau einer WAAM-Fertigungsanlage
Eine WAAM-Zelle besteht aus folgenden Komponenten, von denen einzelne optional sind:
- Kinematik:
- Werkzeugführung: kartesisch oder roboterbasiert zur Führung des Werkzeugs
- Werkstückführung: gegebenenfalls ein Dreh-Kipp-Tisch für das Bauteil/das Substrat
- Steuerung:
- Numerische Echtzeitsteuerung (z.B. Sinumerik von Siemens) zur Steuerung der Kinematik
- Speicherprogrammierbare Steuerung (SPS) um Ein- und Ausgänge zu schalten
- Prozessüberwachung:
- Sensorik (z.B. Stromsensor, Spannungssensor, Spektrometer, Drahtvorschubsensor, Mikrofon, Körperschallsensor, Pyrometer, Schweißkamera, Gasflusssensor)
- Edge-Geräte (z.B. Sinumerik Edge von Siemens von Nvidia Jetson von Nvidia) zur Verarbeitung der Daten
- Sicherheitssystem: Zaun, Notausschalter, Schweißermaske, ...
Weitere Anforderungen an ein WAAM-System sind auch in [2] hinterlegt.
Wertschöpfungskette
Die Wertschöpfungskette besteht aus drei Schritten[1]:
- Die Wertschöpfungskette beginnt beim Bauteildesign im CAD-Umfeld. Es folgt die Prozessplanung mittels CAM-Unterstützung. Zunächst wird der Werkzeugweg angelegt. Dieser kann mithilfe von Temperatur- und Verzugssimulationen überprüft werden. Es folgt eine Maschinensimulation, mit deren Hilfe sichergestellt wird, dass es beim Abfahren der Werkzeugwege zu keinen Kollisionen kommt. Auf Basis der erzeugten Bewegungen der Kinematik wird ein Maschinencode, beispielsweise G Code, erzeugt.
- Mithilfe des G Codes steuert die Echtzeitsteuerung den Fertigungsprozess. Mithilfe der Prozessüberwachung werden prozessparallel relevante Informationen zum Prozess und zum Bauteil aufgenommen und ausgewertet. Gegebenenfalls kann eine Prozessregelung[3] (Seite Datenerfassung und Prozessregelung im WAAM Prozess) eingesetzt werden. Nach der Fertigung findet eine Nachbearbeitung, beispielsweise in Form einer Wärmebehandlung oder einer Bearbeitung der Funktionsflächen, statt.
- Zuletzt erfolgt die Qualitätssicherung. Dafür können beispielsweise Ultraschall- oder Röntgengeräte eingesetzt werden.
Referenzen
- ↑ 1,0 1,1 R.T. Reisch, Prozessorientierter Digitaler Zwilling für die Additive Fertigung mittels Lichtbogenauftragsschweißen, (TUM, 20xx),
- ↑ R.T. Reisch, Robot Based Wire Arc Additive Manufacturing System with Context- Sensitive Multivariate Monitoring Framework, (FAIM, 2020),
- ↑ R.T. Reisch, Nozzle-to-Work Distance Measurement and Control in Wire Arc Additive Manufacturing, (ESSE, 2021),